L’origine du zamak dans l’industrie en France :
Extraits traduits d’après C. A. WAHL / John G. Wolbach Library, Harvard-Smithsonian Center for Astrophysics
Date de publication : Décembre 1949
La période 1910 – 1930 :
« … La fonderie sous pression est un procédé de fonderie mécanique consistant à injecter du métal à l’état liquide et sous pression dans un moule métallique afin de reproduire au retrait près l’empreinte gravée dans le dit moule.
Ce procédé dérive directement de la fonderie en coquille par gravité, mais présente comme avantages :
1° De très fortes cadences de fabrications (une machine moderne Peut effectuer environ 500 injections à l’heure).
2° La suppression presque complète ou complète d’usinage ultérieur.
3° Une très grande précision et de ce fait la possibilité parfaite d’interchangeabilité des pièces coulées.
Ces trois facteurs permettent de très intéressantes réductions dans les prix de revient en facilitant souvent considérablement la réalisation de certaines pièces.
La première application de la fonderie sous pression fût la fabrication de caractères d’imprimerie en alliages plomb-étain. Par la suite et en raison de l’intérêt du procédé, des essais furent tentés pour l’appliquer dans la coulée d’autres pièces. Malheureusement, l’alliage plomb-étain ne pouvait convenir qu’à des réalisations très limitées en raison de ses caractéristiques mécaniques peu élevées.
Le laiton fut alors essayé; malheureusement, ce métal nécessitait des machines très importantes et peu maniables en raison de la forte pression nécessaire. En plus, le moule relativement coûteux se trouvait détérioré après la fabrication de quelques milliers de pièces et ce en raison du haut point de fusion du laiton (900 it 1.000° C.).
Dans ces conditions, le moule ne pouvait être amorti et en raison de manque de fluidité du métal, les usinages ne pouvaient venir complètement de fonderie. Il fallait, par conséquent, pour que la fonderie sous pression prenne son essor trouver un métal qui soit à la fois très fluide et qui coule à basse température. Ce sont les alliages de zinc qui ont le mieux répondu à ces spécifications.
Il fût de ce fait élaboré des alliages de ce type contenant presque tous de l’aluminium, en diverses proportions, du cuivre et même parfois de l’étain.
Ces alliages, à leur début, donnèrent certaines satisfactions, surtout au point de vue facilité de coulée. Ils étaient en effet très fluides et leur point de fusion était seulement de 400° C. environ.
Toutefois, au bout d’un certain temps, il fût possible de constater qu’ils subissaient une certaine déformation, une perte de leurs qualités mécaniques et même parfois une sorte de désintégration. Ce phénomène appelé corrosion inter-cristalline arrêta l’élan que la fonderie sous pression avait pris avec la guerre de 1914 et les alliages de zinc ne furent guère plus utilisés après cette époque que dans les fabrications tout à fait accessoires.
Ce n’est qu’en 1931, après de longues recherches, que les Américains, en l’espèce, la New Jersey Zinc Company, découvrirent que le défaut de vieillissement constaté avec des alliages de zinc provenait d’impuretés nuisibles, surtout le plomb et l’étain contenus normalement dans le zinc.
1931 : l’avènement du Zamak
Ayant précisément découvert le raffinage du zinc par distillation, par reflux, et obtenu de ce fait un zinc titrant : 99,993 % de pureté, ils s’aperçurent que les alliages élaborés à partir de ce zinc ne subissaient plus l’effet de la corrosion inter-cristalline.
La New Jersey Zinc Company fit breveter le principe du zinc extra-pur dans la fabrication des alliages de zinc, rechercha parmi de nombreuses compositions les alliages les meilleurs et finit par s’arrêter aux alliages « Zamak » maintenant universellement connus.
Pratiquement, trois types de Zamak furent retenus : le Zamak 2 contenant en plus du zinc spécial 99,993 % 4 % d’aluminium, 3 % de cuivre, 1 % de magnésium.
Le Zamak 3, identique au précédent, mais sans cuivre. Le Zamak 5, toujours similaire, mais avec 1 % de cuivre. Pratiquement, à l’heure actuelle, ce sont les. alliages Zamak 5 et 3 qui sont les plus utilisés…. »
En France c’est vraisemblablement l’usine parisienne de Citroën qui fabrique pour la 1ère fois des pièces zamak injectées sous pression en grande série nécessaires à l’assemblage de la voiture ‘Traction Avant’, moment capturé en 1934 à l’occasion d’un documentaire filmé et visible encore aujourd’hui avec le lien ci-dessous.
Source : https://youtu.be/z02kvk-sla8
Visible à 7:00 dans le documentaire.
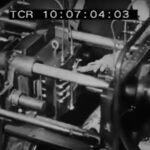